Protecting Your Investment
Modern society depends on infrastructure not only for health and safety benefits, but also to enhance quality of life. As such, maintaining that infrastructure so that it functions as intended is very important. That is why Condition Assessments are so critical to the goal of keeping our infrastructure working properly. Hayter Engineering offers Condition Assessments patterned to evaluate the performance of two key components of modern infrastructure— potable water systems and wastewater systems.
The Condition Assessments that are available from Hayter Engineering for these two key components are as follows:
Is your gravity filter experiencing any of these conditions?
- Increased head loss – increased water level above the filters required during filtration.
- Increased turbidity – the filter effluent turbidity reaches the maximum sooner than usual.
- Increased volume and / or flowrate of backwash water required – to properly clean filter media.
- Uneven filter media surface – humps or depressions forming at the top of the filter media.
- Decrease in overall filter media depth – as measured between the top of the media and the bottom of the backwash trough.
- Increase in overall filter media depth – as measured between the top of the media and the bottom of the backwash trough.
- Decrease in filter bed expansion during backwash – compared to when the filter backwash system was first installed.
- Uneven distribution air scour – parts of the surface show significantly more air bubbles and larger air bubbles than other areas.
A water treatment plant filter assessment by Hayter Engineering may discover one or more of the following filter problems:
- Contamination of the filter media due to mineral precipitation or coagulant accumulation.
- Degradation of the filter media caused by a change in effective size and uniformity coefficient.
- Plugging of the filter underdrain.
- Malfunctioning of the backwash system.
- Malfunctioning of the air scour system.
- Problems with upstream components such as the clarifier or the chemical feed system.
Give us a call at 903.785.0303 to see how we can help you solve your WTP gravity filter issues!
Is your water system pump station experiencing any of the following issues?
- The pumps are noisy – The pumps sound like they are pumping gravel.
- Water hammer occurs when the pumps shut off – The pressure spikes shortly after the pumps turn off and a loud slamming sound occurs.
- Difficult priming – Sometimes the pumps have difficulty starting to pump.
- Impeller wear – Inspection of the impeller shows pitting and unsmooth surfaces.
- Excessive amp draw upon start-up – High amp draw when the pumps turn on is causing breakers to trip and / or high electrical demand charges.
- No provisions for emergency loss of power – Loss of power results in water hammer, with no means of addressing the pressure spike.
- Cloudy or milky-colored discharge water – Water is clear in the ground tanks; but is cloudy or milky in appearance after being pumped into the system.
A water system pump station assessment by Hayter Engineering may lead to the discovery of one or more of the following issues:
- Net Positive Suction Head (NPSH) issues may be causing noisy pump operation under certain conditions.
- Water hammer may be a result of improper check valves, lack of reduced speed stopping, or lack of pressure-absorbing components.
- Air-locking may be the cause of difficulty in pump priming upon start-up under certain situations.
- Improper suction pressure conditions are normally the cause of impeller wear, although sometimes it is a result of abrasive particles in the fluid being pumped.
- Lack of reduced speed starting or lack of reduced flow starting may be the cause of excessive amp draw and power cost when the pumps start up.
- Without devices to manage the water hammer resulting from a sudden loss of power, there is no alternative to the resulting excess pressure.
- Pressure maintenance devices may be causing well water to exceed air saturation levels.
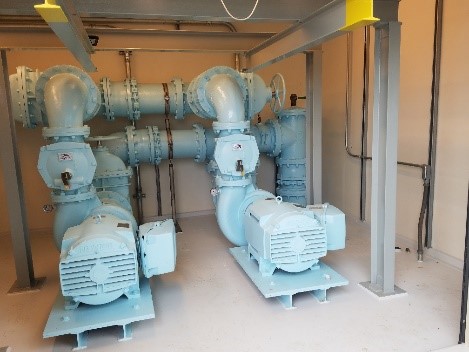
Following the identification of the cause of the problem, Hayter Engineering can provide recommendations to address the issues.
Can Hayter Engineering assist you with any of the following lift station problems?
- Noise during pumping – The pumps make popping noises, or sound like they are pumping gravel.
- Difficulty pumping solids – Rags, hair, rocks, and other solids plug the pumps and damage equipment.
- Intense odor at the force main discharge manhole – Homes and businesses in the immediate area of the discharge manhole complain regularly of the “rotten-egg smell” associated with H2S gas in the pumped sewage.
- Water hammer occurs when the pumps turn off – The pressure spikes shortly after the pumps turn off and a loud slamming sound occurs.
- Difficult priming – Self-priming pumps have difficulty starting to pump.
- Impeller wear – Inspection of the impeller shows pitting and unsmooth surfaces.
Let Hayter Engineering assess your lift station to determine if one or more of the following are causing your lift station problems:
- Self-priming pumps may be experiencing net positive suction head (NPSH) problems if the height of the suction lift is too high and / or suction line size and component restrictions are present.
- Wetwell design limitations, control set-up, piping arrangement, and other issues may be leading to damage associated with the pumping of solid material present in the waste stream.
- Inadequate flushing velocity in the force main, elevated detention times in the wet well, lack of aeration of the wet well contents, and other reasons may contribute to foul odors at the discharge point.
- Excess pressure on the discharge side of the pumps when the pumps turn off may be a result of improper check valve and control set-up.
- Priming difficulties may be due to excessive suction lift. It may also be a result of improper wetwell design.
- Impeller wear may be a result of NPSH problems and / or the material being pumped.
Following our assessment of your lift station, recommendations to address the issues will be provided
Are you experiencing any of the following problems with your water system?
- Excess pressure – Blow-outs on your system and blow-outs on the customer side of the meter are becoming more and more frequent.
- Inadequate pressure – Customer complaints and / or fire hydrants have inadequate flow to meet minimum fire-fighting standards.
- Excessive disinfection by-products (DBP’s) – The running annual average (RAA) of trihalomethanes (TTHM’s) and / or haloacetic acids (HAA5’s) exceeds the regulated maximums.
- Insufficient disinfection residuals – Excessive line flushing and / or fines from the State have become a big concern.
- Excess unaccounted-for water losses – Despite your best efforts, you are having difficulty meeting your target water loss rates due to unidentified line leaks and / or defective meters.
- Too many customers on certain size lines – Growth in the number of meters on small lines has resulted in more customers than is allowed by regulation.
Allow Hayter Engineering to assist you with determining the reasons for your system problems. Some possible reasons for these problems are listed below:
- Lack of properly located pressure reducing valves, or none at all, may result in pressure exceeding safe levels.
- Too many customers on one line, improper pressure maintenance, system expansion into areas of higher elevation and / or further from the pressure source, etc. may contribute to pressure lower than desirable levels.
- Water age, excessive disinfection residual, inadequate or improper flushing, and high organic levels in the source water may all contribute to excess DBP’s.
- Lack of flow-paced control of disinfection or improper control of storage tanks may lead to improper residuals.
- Excess water loss may be the result of excess pressure in the system and / or the age of lines causing line leaks, inaccurate water meters, or water theft.
- Uncontrolled meter installation along small lines may result in having too many meters on that line.
- Years of system changes without adequate documentation often result in records that don’t reflect existing conditions.
- Not using available modern technology to take meter readings means that the resources of the staff are diverted to manual reading and usage entry into the billing software.
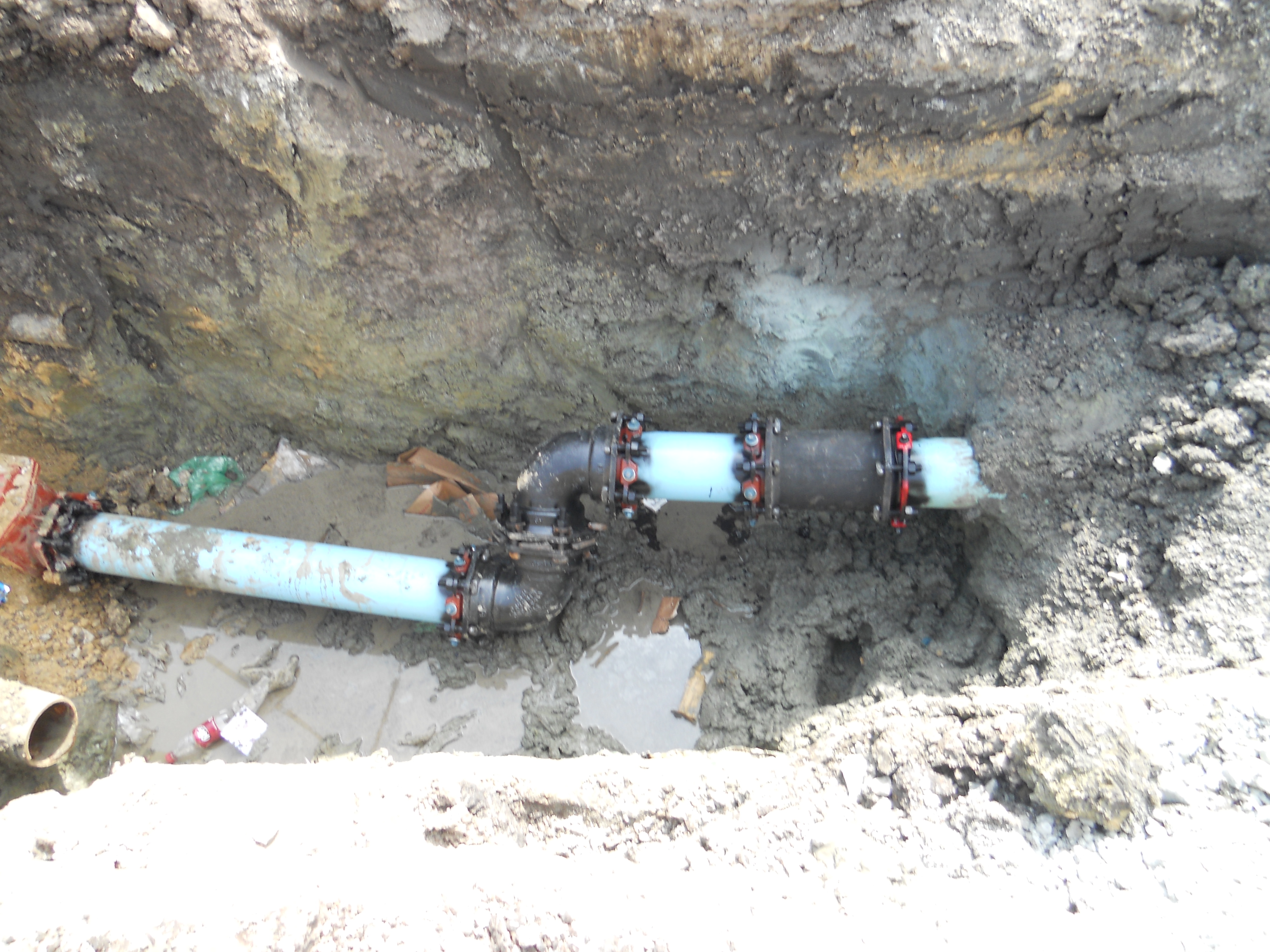
Hayter Engineering can offer recommendations to address these problems so that you have more resources available to address other issues.
Are you experiencing any of these issues at your surface water treatment facility?
- Difficulty in achieving consistent inactivation ratios – Not being able to maintain a consistent inactivation ratio means that control of disinfection residuals and the subsequent DBP formation may be difficult.
- Lack of control over various treatment processes – Not being able to monitor the various parameters (TOC, disinfectant residual, temperature, NTU, pressure, flow, pH, water level, etc.) in real time means that control of the treatment process is much more difficult.
- Improper pump types – A pump that is too big or too small to perform adequately, or a pump that is the wrong type for the application, may lead to treatment difficulties.
- Conformity to regulations – Non-conformance with State regulations concerning clarifier side water depth, detention times, storage volume, production capacity, transfer pump capacity, high service pump capacity and many others may land the owner in trouble with the governing agency.
- Improper meter type – Not having the proper meter not only results in poor flowrate and volume readings; but may also result in difficulties in meeting treatment goals.
- Improper inlet and outlet piping for clearwells – Not having inlet and outlet piping properly designed may limit the plant’s ability to meet inactivation ratios; and may result in loss of disinfection residual with stagnant water issues.
- Taste and odor complaints – T&O problems lead to dissatisfaction from the customers, which may lead to them reporting the facility to the State regulatory agency.
Allow Hayter Engineering the opportunity to assist you with these issues. Possible causes for these problems may be:
- Improper disinfection injection, improper location of injection points, poor baffle factors, and widely varying flowrates may lead to inactivation ratios that are less than consistent.
- Improper piping, valve selection, process monitoring (NTU, pressure, flow, pH, water level, etc.), component sizing, types of process units, and controls may make it difficult to maintain desired levels of treatment.
- Having the wrong type of pump may lead to inefficiencies, plugging, lack of control, and other problems that interfere with efficient attainment of treatment goals.
- If conformity to regulations is not possible with the existing components, a variance may be able to be obtained.
- Many times, changing the type of meter to suit the application is possible. Sometimes, the existing meter can be reused if changes are made to the connected piping.
- Changing the piping to promote circulation in the clearwells is usually possible. The installation of baffles and relocating the overflow structure are also possible.
- Taste and odor complaints could be the result of excess biofilm in the system, toxins from blue / green algae, “turn-over” in the source lake, or issues with the disinfectant.
Let us help you address the problems in your surface water treatment plant.
Are you dealing with any of these issues at your wastewater facility?
- High electric bills
- Excess dissolved oxygen in the treated effluent
- Excess chlorine in the treated effluent
- Grit accumulation in the aeration chambers
- Plugged grit removal equipment
- Trouble meeting TSS limitations
- Excess flow overloads the plant
- Pumping issues
An assessment by Hayter Engineering could determine if the following reasons relate to the problems being experienced:
- Improperly selected components and / or not using the latest technology may be costing more than it should due to power consumption.
- Not adjusting the air to match current conditions may result in having more DO in the effluent than is necessary to meet permit. A lack of oxygen sensors and control equipment may be the cause.
- Not adjusting the chlorine feed rate to match the current effluent flow rate may result in wasted chlorine. Flow-pacing of chlorine feed equipment may allow the proper dosing based on flow rates, thus reducing the cost of chlorine.
- Lack of grit removal, improper grit equipment, by-passing of the unit, or improper operation may be causing unwanted accumulation.
- Improperly designed screening equipment upstream of the grit removal equipment may cause inefficient operation of such equipment.
- Clarifier short-circuiting, lack of baffling, improper removal of sludge, and / or unlevel overflow weirs may be causing solids to exit the unit.
- Lack of equalization basins and / or the lack of controls and equipment necessary to react to high flows may lead to permit violations.
- Pumps not designed for the application to which they have been used is a source of frustration that can lead to increased costs and busted discharge permits.
Are you experiencing these issues with your well water facility?
- Water from your new well has been tested, and determined by the State to be corrosive
- Water is clear coming out of the well, but cloudy when being pumped into distribution
- Well is producing sand each time it is started
- Excess disinfection by-product formation (even when not under the influence of surface water)
- Your chlorinated well water is being added to chloraminated surface water (causing T&O issues)
Hayter Engineering may suggest one of the following solutions to these issues:
- Blend water from an acceptable source to bring the mixture into compliance, or add chemicals to adjust the corrosion parameters
- Modify the pumping controls and / or piping
- Modify piping and controls to flush the initial water produced until it clears up
- Modify the chlorine injection point, add a secondary chlorine injection point, modify concentrations injected, modify control schematic
- Convert the well to chloramines
Allow us to assist you in correcting your well water issues.
Are you dealing with the following collection system problems?
- Excessive inflow
- Excessive infiltration
- Odor complaints near force main discharge manholes
- Backups into homes and businesses during rain storms
- Backups into homes and businesses not during rain storms
- Sinkholes above sewer lines
- Increasing frequency of line stoppages
Hayter Engineering may suggest solutions to these issues:
- Smoke testing and closed-circuit television (CCTV) inspection to identify inflow and infiltration points. Analyze collection system data and pump station run time records to determine the line segments to replace the segments that have the highest inflow and infiltration unit flows.
- Analyze system to determine adequacy of line sizes.
- CCTV inspection can also be used to determine causes of stoppages.
- Increase force main velocity to keep solids in suspension, odor adsorption units at the manhole, chemical addition at the pump station wetwell
- Inspect lines by CCTV, then replace the segments that exhibit inflow and infiltration that is removing trench backfill below the street.
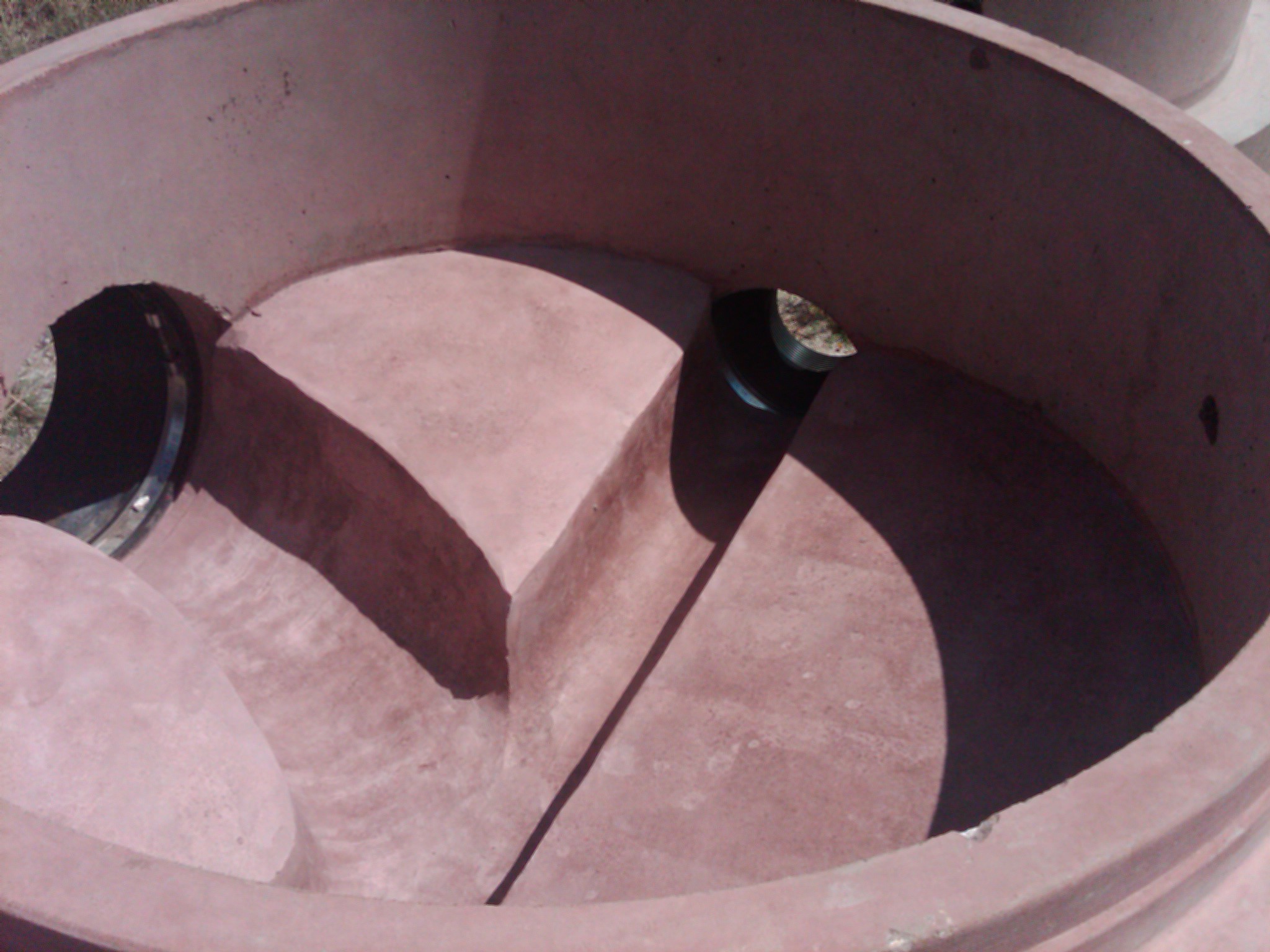
Condition Assessments for these key infrastructure components can be used proactively to search for potential problems before they become emergencies. Condition Assessments can also be used to diagnose problems and to assist in developing recommendations for solutions for these issues.